Case study
Routing locomotives to shops for periodic maintenance
CSX Transportation
As per Federal Railway Administration (FRA) regulations, every locomotive must be sent to a shop for periodic maintenance within 92 days of its previous maintenance. We developed a software solution for CSX Transportation to direct locomotives to shops for this maintenance just-in-time while ensuring consistency with shop capacities and capabilities.
50%
Reduction in the average daily number of past-due-Q locomotives
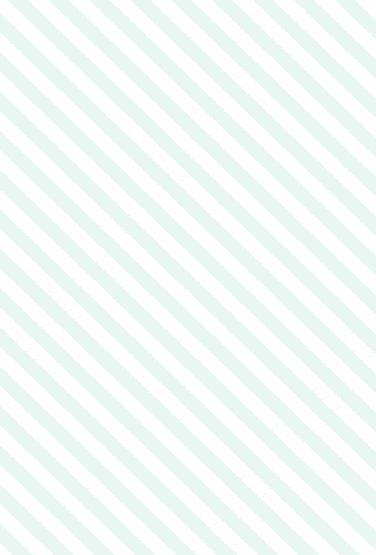
Many locomotives at CSX Transportation were becoming past-due-Q before reaching shops, hurting locomotive productivity.
Business problem
A typical large freight railroad in the United States owns between 4,000 to 8,000 locomotives, each costing millions of dollars. According to Federal Railway Administration (FRA) regulations, every locomotive must be sent to a shop for quarterly maintenance (Q) within 92 days. If a locomotive cannot reach a shop by then, it becomes past-due-Q and is required to be taken out of service. As a result, the locomotive manager is responsible for directing locomotives to shops just-in-time, so the number of locomotives arriving at a shop on the daily basis is consistent with the shop’s capacity and capabilities. CSX faced the following challenge: Many locomotives at CSX Transportation were becoming past-due-Q before reaching shops, hurting locomotive productivity. The company asked Optym to build a real-time decision support system to route locomotives due for quarterly maintenance to shops to reduce the number of past-due-Q locomotives.
Our approach
For several months, we studied CSX’s locomotive movements, shop operations and various types of locomotive maintenances, while visiting several locomotive maintenance shops. Then, we designed and developed optimization algorithms for routing locomotives to shops. For each locomotive scheduled for maintenance within the next week, our system generated recommendations concerning which shop it should visit and what route it should take to that shop over the existing set of scheduled trains.
Since this system generated recommendations (as opposed to requirements), we realized locomotive managers might or might not follow them for any number of reasons. To allow for flexibility in such cases, our system generated a new set of recommendations that factored in locomotive managers’ decisions — much like the rerouting adjustments that a GPS makes when a driver doesn’t follow the map provided by the system. Our system required near real-time data of locomotive and train movements to generate the routing of locomotives to shops. Since the data quality was a challenge in this project, we developed routines for data verification and repair.
Key benefits
- Since this system has gone into production, the average daily number of past-due-Q locomotives has been reduced by about 50%.
- The variance in past-due-Q locomotives from one day to another has also decreased dramatically.
- Since each locomotive incurs several hundred thousand dollars in annual maintenance costs, the system paid for itself within just one year of its deployment.
Results
Thanks to our system, CSX’s locomotives now flow to shops in a more regular fashion from one day to another and in a manner consistent with shop capacities. This reduced the number of cases where some shops received more locomotives than they could maintain, while other shops received too few locomotives.