Case Study 
Using Data to Identify Missed Connection Causes at a Hump Yard
Belt Railway of Chicago
Belt Railway of Chicago (BRC) found that at its Clearing Yard, one of the largest yards in the United States, a large number of its cars were missing their connections from inbound trains to outbound trains. Through data mining, we identified the causes for missed connections and uncovered solutions to address them.
50%+
Decrease in the number of missed connections
3,000+
Cars per day through BRC Clearing Yard
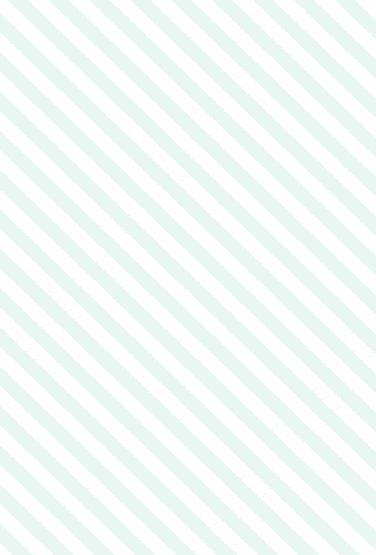
BRC observed that a higher percentage of railcars started missing their connections, which increased the car dwell time in the yard and negatively impacting service quality and yard capacity
Business Problem
Belt Railway of Chicago’s (BRC) Clearing Yard is the largest interchange yard in the United States. It is jointly owned by the six largest freight railroads and enables the exchange of railcars from one railroad to another. Railcars traveling from coast to coast are carried by at least two railroads, while the handover takes place at interchange yards. At these yards, railcars come from inbound trains, are processed, and then depart on outbound trains. BRC observed that a higher percentage of railcars started missing their connections, which increased the car dwell time in the yard and negatively impacting service quality and yard capacity. BRC engaged Optym to analyze the root cause of missed connections and find solutions for these issues.
Our Approach
First, we gathered the data for all car arrivals, departures and other movements within the yard. We collected it for two months during two different years: when missed connections were acceptable and when they were unacceptable. After we prepared the car event database, we used it to prepare histograms and charts for different key performance indicators (KPIs), including car dwell times, car inventory and missed connections. This gave us valuable insight into the yard’s operations.
We correlated different KPIs to establish relationships between them and used these correlations to isolate the causes of the high percentage of missed connections. Once we knew the causes, we delivered straightforward solutions to BRC executives. We worked very closely with the BRC executive team, and the constant exchange of ideas between us greatly improved the quality of project deliverables. Their executives knew exactly what they needed to fix once we found the root cause of the problem.
Key Benefits
- Fixing the root causes decreased the number of missed connections by 50% and brought the total to an acceptable level.
- The BRC Clearing Yard now operates at its peak performance and processes more cars than ever.
- As a result of our data analysis and data mining, we arrived at deep insights into yard operations and how operations in one part of the yard impacted other areas of the facility.
Results
The root cause of missed connections was that the night shift received the largest number of cars, while the morning shift was the slowest in processing cars, due to maintenance activities. Since this resulted in high car inventory in the receiving yard, the cars missed their connections due to delays. We suggested that the priority should be to process these cars as quickly as possible and not let them accumulate in the receiving yard. BRC management issued these instructions to its operations department.